Inventory Management- Inventory management is the process of efficiently and effectively managing a company’s stock of goods. It involves planning, organizing, and controlling the acquisition, storage, and sale of inventory. Effective inventory management is crucial for businesses of all sizes, as it directly impacts profitability, customer satisfaction, and overall operational efficiency.
Key Components of Inventory Management
- Inventory Planning: Determining the optimal quantity and timing of inventory purchases or production.
- Inventory Tracking: Maintaining accurate records of inventory levels, locations, and movements.
- Inventory Storage: Ensuring proper storage conditions to protect inventory from damage or loss.
- Inventory Control: Implementing measures to prevent theft, fraud, and excessive inventory levels.
- Inventory Valuation: Determining the monetary value of inventory for financial reporting purposes.
Importance of Effective Inventory Management
- Improved Cash Flow: Optimal inventory levels can help reduce carrying costs (storage, insurance, etc.) and prevent stockouts.
- Enhanced Customer Satisfaction: Adequate inventory ensures products are available when customers need them, leading to higher customer satisfaction.
- Reduced Costs: Efficient inventory management can minimize waste, spoilage, and obsolescence.
- Better Decision Making: Accurate inventory data enables informed decisions regarding purchasing, production, and pricing.
- Risk Mitigation: Effective inventory management can help mitigate risks such as supply chain disruptions and demand fluctuations.
Common Inventory Management Techniques
- Just-in-Time (JIT): A system that aims to minimize inventory levels by ordering or producing goods only as needed.
- Economic Order Quantity (EOQ): A mathematical model used to determine the optimal order quantity that minimizes total inventory costs.
- ABC Analysis: A method of classifying inventory items based on their value and usage to prioritize management efforts.
- Reorder Point: The minimum inventory level at which a new order should be placed to avoid stockouts.
- Safety Stock: Additional inventory held to buffer against unexpected demand fluctuations or supply chain disruptions.
Inventory Management Systems (ISM)
Modern businesses often rely on Inventory Management Systems (IMS) to automate and streamline inventory processes. These systems can:
- Track inventory levels in real-time.
- Generate purchase orders automatically.
- Monitor stock movements and locations.
- Provide insights into inventory performance and trends.
- Integrate with other business systems like REP and CRAM.
By implementing effective inventory management strategies and leveraging advanced technologies, businesses can optimize their operations, improve profitability, and enhance customer satisfaction.
What is Required Inventory Management
Required Inventory Management: A Comprehensive Guide
Required Inventory Management is a critical aspect of business operations that ensures the availability of necessary goods or materials to meet customer demand and production needs. It involves planning, tracking, and controlling inventory levels to avoid stockouts while minimizing excess inventory.
Key Components of Required Inventory Management:
- Demand Forecasting: Predicting future demand for products or materials based on historical data, market trends, and other relevant factors.
- Inventory Planning: Determining the optimal quantity and timing of inventory purchases or production to meet foretasted demand.
- Inventory Tracking: Maintaining accurate records of inventory levels, locations, and movements to ensure visibility and control.
- Inventory Control: Implementing measures to prevent theft, loss, and damage of inventory, as well as minimizing excess stock.
- Reorder Point: Establishing the minimum inventory level at which a new order should be placed to avoid stock-outs.
- Safety Stock: Maintaining a buffer of inventory to account for unexpected demand fluctuations or supply chain disruptions.
Benefits of Effective Required Inventory Management:
- Improved Customer Satisfaction: Ensuring products are available when customers need them leads to higher satisfaction and loyalty.
- Reduced Costs: Minimizing excess inventory and stockouts can reduce carrying costs and lost sales.
- Enhanced Operational Efficiency: Accurate inventory data enables better production planning and resource allocation.
- Better Decision Making: Informed inventory management decisions support strategic planning and risk mitigation.
- Improved Cash Flow: Efficient inventory management can help optimize working capital by reducing the amount of money tied up in inventory.
Challenges in Required Inventory Management:
- Demand Uncertainty: Fluctuations in customer demand can make it difficult to accurately forecast inventory needs.
- Supply Chain Disruptions: Unexpected events like natural disasters, supplier issues, or transportation problems can impact inventory availability.
- Product Obsolescence: Changes in technology or consumer preferences can lead to obsolete inventory.
- Inventory Costs: Carrying costs (storage, insurance, etc.) can be significant, especially for high-value or perishable items.
Best Practices for Required Inventory Management:
- Use Forecasting Tools: Employ accurate forecasting methods to anticipate demand changes.
- Implement Inventory Control Systems: Utilize technology to track and manage inventory effectively.
- Optimize Reorder Points: Regularly review and adjust reorder points to match demand patterns.
- Manage Safety Stock: Maintain appropriate safety stock levels based on risk tolerance and demand variability.
- Regularly Review Inventory: Conduct periodic reviews to identify slow-moving or obsolete items.
- Consider Inventory Optimization Techniques: Explore methods like ABC analysis, just-in-time (JIT), and economic order quantity (EOQ) to optimize inventory levels.
By effectively managing required inventory, businesses can improve their overall efficiency, profitability, and customer satisfaction.
Who is Required Inventory Management
Inventory management is a critical process for businesses of all sizes. It involves the effective planning, control, and coordination of the acquisition, storage, and distribution of inventory. While not everyone within a company may be directly responsible for inventory management, it’s a task that impacts a wide range of departments and individuals.
1. What is Inventory Management? – IBM
Here are some key roles that are directly or indirectly involved in inventory management:
- Purchasing or Procurement: These departments are responsible for acquiring inventory, whether it’s raw materials, finished goods, or components. They need to ensure that the right quantities are ordered at the right time to meet production and sales needs. 1. Who Is Responsible for Inventory Control in a Store? | Alice POS alicepos.com
- Inventory Control: This specific role focuses on tracking and managing inventory levels. They use various methods, such as bar-coding, RAID, or inventory management software, to monitor stock levels, identify discrepancies, and ensure accuracy. 1. Inventory Control Defined: Best Practices, Systems, & Management – NetSuite www.netsuite.com
- Warehouse Management: Warehouse personnel are responsible for storing and handling inventory. They need to ensure that products are stored correctly, safely, and efficiently to prevent damage or loss. 1. Essential Warehouse Positions: Roles and Responsibilities – Cyzerg cyzerg.com
- Production Planning: In manufacturing companies, production planners need to have a clear understanding of inventory levels to schedule production runs effectively. They need to ensure that there are sufficient raw materials and components available to meet production targets. 1. What Does a Production Planner Do? – SNHU www.snhu.edu
- Sales and Marketing: Sales and marketing teams need to be aware of inventory levels to avoid overselling or underselling products. They can use inventory data to make informed decisions about product availability and pricing. 1. Impact of Real-Time Inventory in your Sales Process – Onpipeline www.onpipeline.com
- Finance: The finance department is responsible for tracking inventory costs and managing inventory-related assets. They need to ensure that inventory is accounted for accurately and that inventory-related expenses are controlled.
In essence, effective inventory management requires collaboration and coordination among various departments and individuals within an organization. By working together, they can ensure that the right products are in the right place at the right time, minimizing costs and maximizing customer satisfaction.
When is Required Inventory Management

Required Inventory Management is a continuous process that needs to be implemented and monitored throughout the year. It’s not a one-time event or a seasonal activity.
Here are some key times when required inventory management becomes particularly important:
- During Peak Seasons: When demand for products or services is significantly higher than usual, such as holidays or special events, inventory management becomes crucial to ensure adequate stock levels.
- When Introducing New Products: Launching new products often requires careful inventory planning to avoid stock-outs or overstocking.
- During Supply Chain Disruptions: In the event of unexpected supply chain issues, such as supplier delays or transportation problems, effective inventory management is essential to minimize disruptions and maintain product availability.
- When Reviewing Inventory Performance: Regular reviews of inventory levels, turnover rates, and carrying costs help identify areas for improvement and optimize inventory management practices.
- During Economic Fluctuations: Changes in economic conditions can impact demand for products and services. Inventory management needs to be adjusted accordingly to avoid overstocking or shortages.
Overall, required inventory management is a vital ongoing task that helps businesses maintain operational efficiency, improve customer satisfaction, and optimize profitability.
Where is Required Inventory Management
Required Inventory Management is a term that can refer to a few different things, depending on the context:
- A specific software or tool: If you’re referring to a particular software application designed for inventory management, it might be found on the website of the software provider or through online marketplaces.
- A concept or process: If you’re referring to the general idea of managing inventory, it’s a fundamental aspect of business operations that can be implemented through various methods, including manual tracking, spreadsheets, or dedicated software. 1. Inventory Control Defined: Best Practices, Systems, & Management – NetSuite www.netsuite.com
If you can provide more context about what you’re looking for, such as:
- The industry or type of business (e.g., retail, manufacturing, healthcare)
- Specific tasks or challenges you’re trying to address with inventory management
- Whether you’re seeking software recommendations or general information
I can provide a more tailored and helpful response.
Here are some resources that might be helpful:
- NetSuite: A popular enterprise resource planning (ERP) software that includes inventory management features. 1. NetSuite Applications Suite – Items and Inventory Features – Oracle Help Center docs.oracle.com
- Inventory Management Software: A general overview of different types of inventory management software.
- Investopedia: An article on inventory management concepts and methods. 1. Inventory Management: Definition, How It Works, Methods & Examples – Investopedia www.investopedia.com
Please let me know if you have any other questions.
How is Required Inventory Management
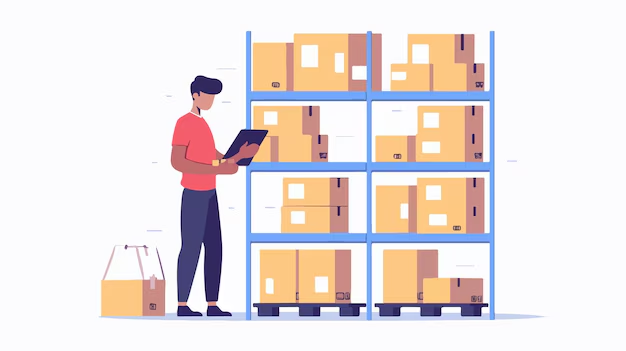
Required Inventory Management is typically implemented through a combination of manual processes, spreadsheets, and specialized software systems. Here’s a breakdown of the common methods:
Manual Processes:
- Visual Inspections: Regularly checking inventory levels and storage areas to identify shortages or excesses.
- Physical Counts: Periodically counting inventory items to verify accuracy.
- Manual Record Keeping: Maintaining inventory records using spreadsheets or physical files.
Spreadsheets:
- Inventory Tracking: Using spreadsheets to track inventory levels, locations, and movements.
- Demand Forecasting: Creating simple forecasting models to predict future demand.
- Reorder Point Calculations: Calculating reorder points based on demand and lead times.
Inventory Management Software:
- Enterprise Resource Planning (ERP) Systems: Integrated systems that include inventory management modules.
- Warehouse Management Systems (WMS): Specialized software for managing warehouse operations and inventory.
- Supply Chain Management (SCM) Systems: Systems that optimize the flow of goods and materials throughout the supply chain.
These methods can be used individually or in combination, depending on the size and complexity of the business. More advanced businesses often rely on software systems to automate inventory management processes and provide real-time visibility into inventory levels and movements.
Case Study on Inventory Management
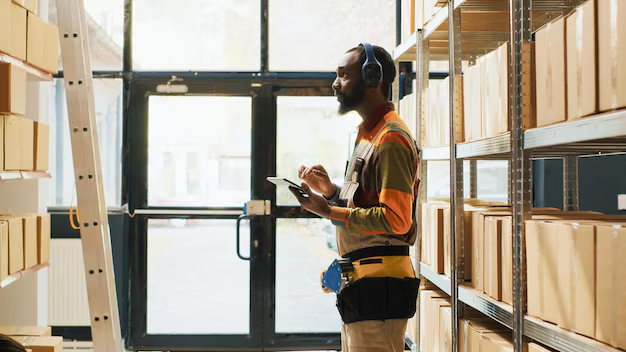
Acme Corporation is a mid-sized manufacturing company that produces a variety of electronic components. In recent years, the company has faced challenges with inventory management, including stock-outs, excess inventory, and high carrying costs.
Problem:
- Stockouts: Frequent shortages of critical components were leading to production delays and lost sales.
- Excess Inventory: Overstocking of slow-moving items was tying up capital and increasing storage costs.
- High Carrying Costs: The cost of storing and managing inventory was a significant burden on the company’s profitability.
Analysis:
- Demand Variability: Acme’s products experienced significant fluctuations in demand, making it difficult to accurately forecast inventory needs.
- Inefficient Inventory Tracking: Manual processes and outdated systems were leading to inaccurate inventory records and delays in identifying stock-outs or excesses.
- Lack of Standardization: The company had a lack of standardized procedures for inventory management, resulting in inconsistencies and inefficiencies.
Solution:
- Implement an Inventory Management System (IMS): Acme invested in a modern IMS to automate inventory tracking, forecasting, and ordering processes.
- Improve Demand Forecasting: The company implemented statistical forecasting techniques to better predict demand for its products.
- Optimize Reorder Points: Reorder points were adjusted based on demand variability and lead times to minimize stockouts and excesses.
- ABC Analysis: Inventory items were classified using ABC analysis to prioritize management efforts and allocate resources more effectively.
- Lean Manufacturing Principles: Lean principles were adopted to reduce waste and improve inventory flow.
Results:
- Reduced Stock-outs: The implementation of an ISM and improved forecasting led to a significant reduction in stock-outs.
- Optimized Inventory Levels: By optimizing reorder points and using ABC analysis, Acme was able to maintain appropriate inventory levels while minimizing excess stock.
- Lower Carrying Costs: The reduction in excess inventory and improved inventory management practices resulted in lower carrying costs.
- Improved Customer Satisfaction: The increased availability of products led to higher customer satisfaction and repeat business.
- Enhanced Operational Efficiency: The implementation of lean principles streamlined production processes and reduced waste, leading to improved overall efficiency.
Lessons Learned:
- Invest in Technology: A modern inventory management system is essential for effective inventory control and optimization.
- Improve Forecasting: Accurate demand forecasting is crucial for avoiding stockouts and excesses.
- Optimize Inventory Levels: Use techniques like reorder points and ABC analysis to balance inventory levels.
- Continuous Improvement: Inventory management is an ongoing process that requires regular review and adjustment.
- Leverage Lean Principles: Lean manufacturing can help reduce waste and improve inventory flow.
By addressing its inventory management challenges, Acme Corporation was able to improve its operational efficiency, reduce costs, and enhance customer satisfaction. This case study demonstrates the importance of effective inventory management for businesses of all sizes.
White paper on Inventory Management
White Paper: Optimizing Inventory Management for Enhanced Business Performance
Introduction
Inventory management is a critical function within any organization, directly impacting profitability, customer satisfaction, and operational efficiency. Effective inventory management involves balancing the need to have sufficient stock to meet demand while minimizing excess inventory that can tie up capital and increase costs. This white paper explores key strategies and best practices for optimizing inventory management to drive business success.
Understanding the Importance of Inventory Management
- Improved Customer Satisfaction: Adequate inventory levels ensure products are available when customers need them, leading to higher satisfaction and loyalty.
- Reduced Costs: Minimizing excess inventory and stockouts can reduce carrying costs and lost sales.
- Enhanced Operational Efficiency: Accurate inventory data enables better production planning and resource allocation.
- Better Decision Making: Informed inventory management decisions support strategic planning and risk mitigation.
- Improved Cash Flow: Efficient inventory management can help optimize working capital by reducing the amount of money tied up in inventory.
Key Strategies for Optimizing Inventory Management
- Demand Forecasting:
- Use accurate forecasting methods to anticipate demand changes.
- Consider historical data, market trends, and seasonal factors.
- Employ statistical techniques like time series analysis or regression analysis.
- Inventory Control Systems:
- Implement robust inventory control systems to track and manage inventory effectively.
- Use barcode scanning or RFID technology for real-time visibility.
- Integrate inventory management with other business systems like ERP and CRM.
- Reorder Point Optimization:
- Establish appropriate reorder points to avoid stockouts while minimizing excess inventory.
- Consider lead times, demand variability, and safety stock requirements.
- Regularly review and adjust reorder points based on changing conditions.
- Safety Stock Management:
- Determine optimal safety stock levels to buffer against unexpected demand fluctuations or supply chain disruptions.
- Use statistical models to calculate safety stock based on demand variability and service level requirements.
- Regularly review and adjust safety stock levels as needed.
- Inventory Turnover Analysis:
- Calculate inventory turnover rates to assess the efficiency of inventory management.
- Identify slow-moving or obsolete items that may require adjustments to inventory policies.
- Implement strategies to reduce excess inventory and improve turnover.
- ABC Analysis:
- Classify inventory items based on their value and usage to prioritize management efforts.
- Allocate resources accordingly to focus on high-value items that require more attention.
- Implement strategies to reduce the inventory levels of low-value items.
- Lean Inventory Principles:
- Apply lean manufacturing principles to minimize waste and improve inventory flow.
- Implement just-in-time (JIT) inventory systems to reduce excess stock.
- Focus on continuous improvement to identify and eliminate waste.
Conclusion
Optimizing inventory management is essential for businesses of all sizes to improve profitability, customer satisfaction, and operational efficiency. By implementing the strategies outlined in this white paper, organizations can achieve better inventory control, reduce costs, and enhance their overall business performance.
[Insert relevant case studies or statistics to support the points made in the white paper]
Industrial Application of Inventory Management
Inventory management plays a pivotal role in various industrial sectors, ensuring efficient operations, cost reduction, and customer satisfaction. Here are some key industrial applications:
Manufacturing
- Raw Material Management: Ensuring a steady supply of raw materials to meet production schedules.
- Work-in-Process (WIP) Control: Managing the flow of partially completed products through the manufacturing process.
- Finished Goods Inventory: Maintaining optimal levels of finished products to meet customer demand.
- Just-in-Time (JIT) Inventory: Implementing JIT systems to minimize inventory levels and reduce waste.
Retail
- Product Assortment: Ensuring the availability of a wide range of products to meet customer preferences.
- Demand Forecasting: Predicting sales trends to optimize inventory levels.
- Seasonal Inventory: Managing inventory fluctuations based on seasonal demand patterns.
- Loss Prevention: Implementing measures to prevent theft, shrinkage, and damage.
Healthcare
- Pharmaceutical Inventory: Managing the storage and distribution of medications and medical supplies.
- Expiration Date Tracking: Ensuring compliance with expiration dates to prevent the use of outdated products.
- Emergency Preparedness: Maintaining sufficient inventory levels to meet emergency needs.
Automotive
- Parts Inventory: Managing the inventory of spare parts for vehicle maintenance and repair.
- Supply Chain Coordination: Coordinating inventory levels with suppliers and distributors to ensure timely delivery.
- Vehicle Assembly: Ensuring the availability of components for vehicle assembly.
Electronics
- Component Sourcing: Procuring electronic components from various suppliers.
- Obsolescence Management: Managing the risk of components becoming obsolete.
- Quality Control: Ensuring the quality of electronic components and preventing defective products.
Food and Beverage
- Perishable Goods: Managing the inventory of perishable products like fresh produce and dairy.
- Food Safety: Adhering to food safety regulations and preventing foodborne illnesses.
- Traceability: Tracking the origin and movement of food products for quality assurance.
Logistics and Distribution
- Warehouse Management: Optimizing warehouse operations to minimize storage costs and improve efficiency.
- Transportation Planning: Coordinating inventory movements with transportation schedules.
- Reverse Logistics: Managing the return and recycling of products.
These are just a few examples of how inventory management is applied in various industries. The specific requirements and challenges of each industry may vary, but the underlying principles of effective inventory management remain the same.